Increased put on and oxidation resistance of titanium aluminide alloys by laser cladding Euro Superalloys. Increased wear and oxidation resistance of titanium aluminide alloys by laser cladding. A structured separating layer, consisting of a three-layer vapour-permeable roof underlay membrane with self-adhesive butyl strips, bonded to monofilaments arranged in a random network, for use as a spacer layer between the roof structure and the metal cladding. Those areas subjected to excessive heat - from the exhaust manifold or catalytic converter for example - could be insulated by a refractory materials and metallic cladding. Wire-based mostly laser deposition welding is a cloth-environment friendly 3D printing process for the production of metallic components.
Once the pellet/clad hole is closed, any change in pellet dimensions causes stress within the cladding and the synergy between the stress and the corroding medium induces the SCC process. In order to prevent or reduce pellet/clad interactions, each mechanical and chemical, a coating of graphite powder is applied on the inner floor of cladding tubes.
laser. The clad substrates showed improved oxidation characteristics compared with the original alloy. Conventional strategies for cladding have employed tungsten-inert gas welding, plasma spraying, and flame spraying.
The complete melting of the filler leads to a dense layer with optimal adhesion to the substrate. The most typical utility is for the wear and tear safety, e.g. of instruments, but additionally corrosion protection or high temperature resistance could be particularly improved. Common hard alloys primarily based on cobalt, nickel and iron are used with and with out the addition of onerous materials. But additionally specifically adapted supplies may be applied.
This method is adopted for zircaloy-clad fuels from energy reactors and chrome steel-clad fast reactor fuels. Like the cladding , under the impact of neutron flux the hexagonal wrapper tube undergoes change. Geometrical adjustments, induced by swelling and irradiation creep (beneath the effect of dynamic sodium stress), concern size, throughout-flat dimension, and, for subassemblies positioned in the periphery of the core, bowing (differential swelling induced by differential flux and temperature between opposite faces of the wrapper tube).

Materials
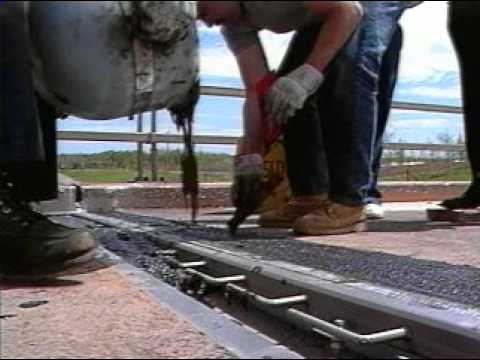
The process is often used to create a protective coating for increased performance, as well as restore damaged or worn surfaces. Laser cladding permits prolonged life of kit and equipment during which parts are exposed to corrosion, put on or influence. For example, the development equipment trade applies this know-how to their merchandise to increase put on resistance and keep gear in service longer. A high-energy laser is used as the warmth supply in laser cladding. During the method, a floor layer is created by the use of melting and the simultaneous utility of virtually any given material.
Moreover, embrittlement owing to irradiation or temperature must be mastered in order to keep away from rupture in the reactor or in the course of the again-finish of the cycle (dealing with, washing, and so forth.). Cold-labored austenitic steels (with composition closed to that of the cladding) were used first however are actually frequently changed by more swelling-resistant ferritic–martensitic steels (9Cr sort), in so far as the peak wrapper temperature, lower than that of cladding, allows avoidance of thermal creep problems.
Our vast range of merchandise includes PVC wall panels, exterior wall cladding, waterproof flooring as an alternative choice to laminate or LVT, waterproof bathe and bathroom panels and far more. These embody cladding, small metallic pins coupled with a ceramic mass, half-pipes and SiC tiles, in addition to numerous types of coatings, together with thermal spray coatings. Its characteristic function is the sash bar down the middle of the window and black (similar to RAL 9005) metal cladding coverings on the window and flashing which matches traditional buildings. The Independent Expert Advisory Panel additionally suggested the department to establish a research challenge to test and enhance the proof obtainable on the behaviour of a range of non-ACM supplies used in cladding techniques when subjected to fireside.
For the identical external loading, the stress produced within the cladding, either exterior from the coolant or inner from fission-product swelling of the gasoline, is decreased in proportion to the wall thickness. However, thick cladding is detrimental to neutron economic system, increases the amount of the reactor core, raises gas temperature, and prices greater than skinny-walled tubing.
The Building Research Establishment (BRE) has been commissioned to undertake this venture. This programme is on-going and tests are expected to conclude in the summertime.
In addition to metallurgical elements, water chemistry has a robust affect on the corrosion course of in zirconium alloys. The management of water chemistry as required in several reactor methods embrace suitable additions of lithium hydroxide, boric acid, hydrogen/deuterium, oxygen, iron, and zinc. In PWRs, boric acid is added to the coolant water for reactivity control. The pH of the coolant is adjusted by addition of lithium hydroxide which renders the coolant barely alkaline, so as to cut back the corrosion charges of structural materials (stainless steels and Inconels) within the main heat transport circuit and thereby inhibit deposition of corrosion products on the fuel cladding. Radiolysis of water produces oxidizing species which enhances oxidation fee of zirconium alloys in the radiation surroundings .
tube. Energy, from fission, is generated roughly uniformly all through the gasoline pellets. Heat is extracted at the rod surface by the coolant move. The temperature at the hottest point, at the pellet centerline, is typically in the vary 800–1000 °C, depending on the facility degree. The metallic cladding is a good conductor, so the temperature rise throughout the wall is only a few tens of levels.
Outside Wall Cladding
The oxidation process and the nature of the oxide layer on a zirconium alloy sample are schematically illustrated in Fig. 6 . Cladding is an outer layer of either vertical or horizontal materials, used to enhance the appearance, thermal insulation and the weather resistance of a building. Our cladding is available in a wide range of sizes, types of timber and floor finishes.
Once the pellet/clad gap is closed, any change in pellet dimensions causes stress in the cladding and the synergy between the stress and the corroding medium induces the SCC process. In order to stop or decrease pellet/clad interactions, both mechanical and chemical, a coating of graphite powder is utilized on the inner surface of cladding tubes.
The thickness of the cladding might range between zero.1 and 30 mm and the detonation velocity is between 1200 and 7000 ms −1 . The prime plate hits the underside plate with a speed of 100–a thousand ms −1 , and pressures are within the range of 10 to 100 kbar. Under certain conditions a superheated layer of material varieties in the contact area. The joint is then attributable to a deformation-induced melting bath.
The constants a and b are primary properties of the fabric and may be decided from normal laboratory experiments on contemporary gas. In explosive welding, a compression force created by detonation of explosives is used to hitch overlapping metallic sheets. The joining parts are organized in direction of one another at an angle of 1–15°, depending on the material and technique, and are prepared with a layer of explosive on the top. After ignition the joining areas are moved against each other at excessive velocity.
The helium filling gas can be a reasonably good conductor, but only so long as it remains uncontaminated by fission merchandise. The poorly conducting ceramic gas pellets are responsible for the majority of the temperature rise. The evolution of the conductivities of the pellet and filling fuel decide how the thermal efficiency develops with burnup.
Zircaloys additionally undergo from unhealthy creep charges. In distinction to floor-layer welding, explosive welding causes no change in microstructure, and corrosion resistance of the layers just isn't affected (Pocalco 1987 ).
The graphite layer provides lubrication to reduce the mechanical interactions, and acts as a barrier against the migration of dangerous species to confused areas of gas tubes. The authentic purpose of tin in Zry was to mitigate the lack of corrosion resistance attributable to pickup of impurity nitrogen during fabrication of the alloy.
These approaches have encountered problems, together with porosity of the cladding, uneven cladding thickness, dilution of the cladding alloy due to the massive heat input required, and distortion of the workpiece by the high warmth input. Laser cladding has decreased these problems and produced cladding layers with good uniformity, good dimensional control, and minimal dilution of the cladding alloy. gives a survey of a cladding gear. If the incoming strips have to be heated in order to decrease the strength of supplies, this has to be carried out as shut as attainable to the rolling hole and in a protective environment so as to avoid oxidation of the cleaned and roughened surfaces. We present high-quality decorative products that improve any home and interior.
Depending on the supplies to be bonded, cleaning and roughening are best accomplished by brushing, grinding, or scraping using a specifically designed cutter with needles. A suction removal unit is used to evacuate rigorously any material waste in order to keep away from bonding flaws as a result of poor adhesion. Laser cladding enables us to apply metallic layers for put on and corrosion protection with great precision. In addition, it can be used to restore and modify parts.

sheet this metal cladding news n How Much Is Cladding For House —

Zircaloys additionally undergo from dangerous creep charges. In contrast to floor-layer welding, explosive welding causes no change in microstructure, and corrosion resistance of the layers just isn't affected (Pocalco 1987 ).
The impact of thermal conductivity degradation on the performance of the gas is illustrated in Fig. 1 . This shows the outcomes of calculations by which the power in a rod is artificially held at a relentless level.
The ensuing cladding layer was properly bonded, and the blades exhibited improved fatigue traits in contrast with blades formed by the traditional silver brazing course of. laser beam. The alloy was overlaid on the metal as a powder layer 2.5 mm thick. After melting and bonding by the laser, the alloy layer was 1.5 mm thick and had little or no dilution from the steel. The resulting floor had wonderful put on resistance.
Moreover, embrittlement owing to irradiation or temperature must be mastered to be able to keep away from rupture in the reactor or during the again-finish of the cycle (dealing with, washing, and so forth.). Cold-worked austenitic steels (with composition closed to that of the cladding) were used first however are actually regularly changed by extra swelling-resistant ferritic–martensitic steels (9Cr kind), in so far as the height wrapper temperature, lower than that of cladding, allows avoidance of thermal creep problems.
Our huge range of products includes PVC wall panels, outside wall cladding, waterproof flooring as a substitute for laminate or LVT, waterproof shower and bathroom panels and far more. These include cladding, small steel pins coupled with a ceramic mass, half-pipes and SiC tiles, as well as varied types of coatings, including thermal spray coatings. Its attribute characteristic is the sash bar down the middle of the window and black (much like RAL 9005) metallic cladding coverings on the window and flashing which matches conventional buildings. The Independent Expert Advisory Panel also suggested the division to establish a research venture to check and enhance the proof available on the behaviour of a spread of non-ACM supplies used in cladding techniques when subjected to fire.
is produced and the chance of a large secondary hydriding failure is elevated. In response to this unforeseen consequence, several fixes have been introduced.
Alloying elements, significantly tin, niobium, and iron, current in the α-stable solution strongly influence each the kinetics and the mechanism of oxide development in zirconium alloys. ions from the surroundings to the reaction entrance at the metal/oxide boundary.
Depending on the supplies to be bonded, cleansing and roughening are best carried out by brushing, grinding, or scraping utilizing a specifically designed cutter with needles. A suction removing unit is used to evacuate rigorously any materials waste to be able to avoid bonding flaws as a result of poor adhesion. Laser cladding allows us to apply steel layers for put on and corrosion safety with nice precision. In addition, it may be used to repair and modify parts.
For the same exterior loading, the stress produced in the cladding, both exterior from the coolant or internal from fission-product swelling of the fuel, is lowered in proportion to the wall thickness. However, thick cladding is detrimental to neutron economic system, will increase the volume of the reactor core, raises gas temperature, and prices greater than thin-walled tubing.